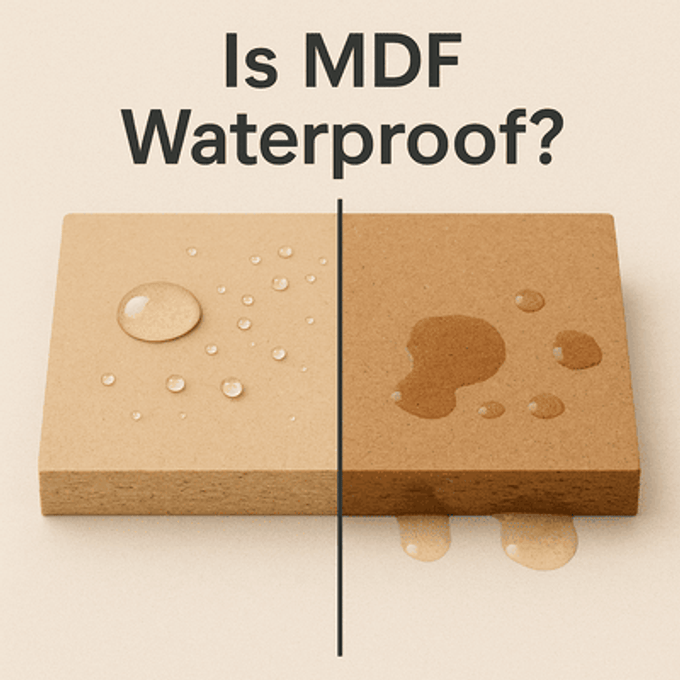
Is MDF Waterproof? | Sealing With Paint | Green MDF
Posted by Skirting World on 23rd May 2025
MDF (Medium Density Fibreboard) isn't waterproof. This fundamental limitation affects how and where you can use it, particularly in kitchens, bathrooms, and other areas where moisture might be present.
Understanding MDF's relationship with water helps you make informed decisions about material selection and protection methods. While standard MDF is vulnerable to moisture damage, there are grades designed for humid conditions and treatments that can improve its resistance.
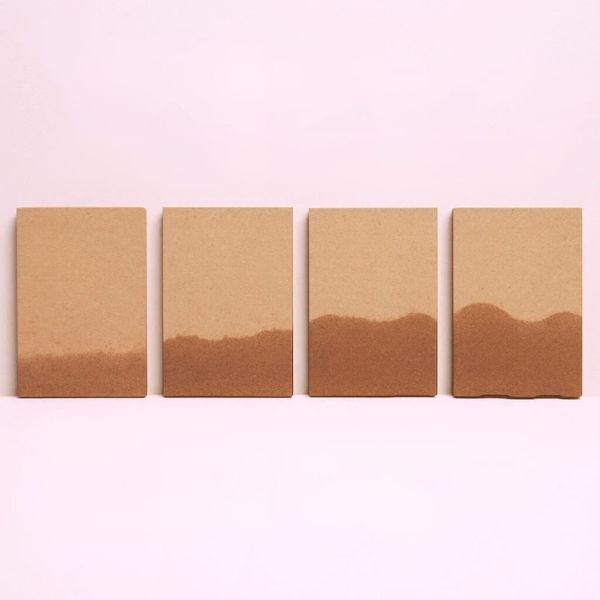
Why isn't MDF waterproof?
MDF consists of wood fibres broken down to their smallest components and reformed with resin under heat and pressure. This manufacturing process creates a smooth, uniform material ideal for many applications, but it also makes MDF particularly susceptible to moisture damage.
The wood fibres in MDF are hygroscopic – they naturally absorb moisture from their environment. Standard MDF uses urea-formaldehyde (UF) resin as a binder, which provides good adhesion in dry conditions but isn't waterproof. When exposed to moisture, this resin can actually break down through hydrolysis, weakening the bonds between fibres.
Standard MDF Composition:
- 82-87% wood fibres (the water absorbers)
- 9-11% UF resin (breaks down when wet)
- 8-9% residual moisture
- 1-2% paraffin wax (minimal water resistance)
Cut edges present the greatest vulnerability. While the manufacturing process creates relatively dense surfaces, cutting exposes the internal fibre structure. These exposed fibres act like countless tiny straws, drawing water deep into the board through capillary action.
Every cut, drill hole, or routed edge in MDF creates a new vulnerability. Unlike solid wood where you can identify and seal end grain, MDF's entire structure consists of randomly oriented fibres ready to absorb moisture.
How water damages MDF
Water damage to MDF occurs rapidly and is largely irreversible. The absorption process begins immediately upon contact, with visible effects often appearing within hours.
Thickness swelling data
Standard testing (EN 317) measures thickness swelling after 24 hours of water immersion. The results demonstrate significant differences between material types:
24-Hour Water Immersion Test Results
Source: EN 317 standardised testing data
For an 18mm MDF board, 15% swelling means an increase to over 20mm – enough to cause cabinet doors to bind, drawer fronts to jam, and joints to fail completely.
Permanent damage
The most problematic aspect of water damage to MDF is its permanence. Once the fibres have swollen and the resin bonds have been compromised, drying doesn't restore the original dimensions or strength. Typical residual swelling after drying ranges from 2-5%, meaning a water-damaged board remains permanently thicker and structurally weaker.
Initial exposure (0-24 hours)
- Edges begin swelling within minutes
- Surface feels raised or bumpy
- Visible thickness increase develops
Extended exposure (24-72 hours)
- Board becomes soft and spongy
- Internal bond strength fails
- Surface coatings delaminate
After drying
- Permanent thickness increase remains
- Surface texture rough and fuzzy
- Structural integrity compromised
Moisture-resistant MDF explained
Moisture-resistant MDF (MR MDF) offers improved performance in humid conditions through modifications to its resin system and additive content. Often identified by green dye added during manufacture, though the colour itself provides no protective properties.
Technical improvements
MR MDF replaces standard urea-formaldehyde resin with melamine-urea-formaldehyde (MUF) or similar moisture-resistant resins. These modified binders offer better resistance to hydrolysis and maintain stronger bonds in humid conditions. The paraffin wax content is also increased, providing additional water repellency to the fibres.
MR MDF performance standards
Classification: EN 622-5 Type MDF.H (general use, humid conditions) or MDF.HLS (load-bearing, humid conditions)
Thickness swelling: 7-12% (EN 317, 24-hour immersion)
Cyclic test: Must retain specified internal bond strength after EN 321 test (immersion, freezing, drying cycles)
Use class: Suitable for EN 335 Use Class 2 (interior, risk of occasional wetting)
Important limitations
Despite its name, moisture-resistant MDF is not waterproof. The improvements allow it to handle high humidity and occasional water contact better than standard MDF, but it cannot withstand prolonged or direct water exposure.
Critical distinction: MR MDF is designed for humid interior conditions like kitchens and bathrooms with good ventilation. It remains unsuitable for exterior use, shower enclosures, or areas with standing water. Even in approved applications, all surfaces and edges must be properly sealed.

Protecting MDF from moisture
Since MDF cannot be made truly waterproof, protection relies on creating effective barriers between the material and moisture sources. Success depends on thorough preparation and appropriate treatment selection.
"There really is only one way to make MDF waterproof: make it so that the water or moisture cannot reach the MDF. So fully encapsulate in resin, paint, caulk, what have you. No holes in the MDF, no screws as they will cause leaks in the encapsulation."
– Online woodworking forum comment
Edge sealing techniques
Cut edges require particular attention as they absorb moisture most readily. Several effective methods exist:
- Oil-based primer: Apply 2-3 coats, sanding lightly between applications. Penetrates deeply into the fibre structure.
- Shellac-based primer: Excellent sealing properties with rapid drying. Builds effective moisture barrier through multiple coats.
- Wood filler: Fill and sand edges smooth before priming. Creates the most durable edge seal.
- PVA glue: Diluted 50/50 with water, multiple coats. Budget option requiring careful application.
"Shellac based primer, a few coats. Make sure you paint every single surface because water will find the one single exposed fibre and draw into the material."
– Experienced DIY comment
Surface finishing systems
After edge sealing, appropriate surface finishes provide the primary moisture barrier:
Using Screws & Nails
Every penetration through the protective coating creates a potential failure point. Screw holes, hinge recesses, and handle cutouts all require sealing before hardware installation. Even small oversights can lead to localised swelling and progressive damage.
"Surface moisture isn't the death sentence that people make it out to be. Inundation is. Use tile spacers under baseboard and leveling feet for cabinets. Leave a good 1/16" of breathing room."
– Practical installation advice
Where to use different MDF types
Selecting the appropriate MDF grade for each application prevents problems and ensures longevity. The key is matching material capabilities to environmental conditions.
Location | Standard MDF | MR MDF | Critical Considerations |
---|---|---|---|
Bathroom - Well Ventilated | ✗ Not Recommended | ✓ With Full Sealing | Extractor fan essential; avoid floor contact |
Bathroom - Poor Ventilation | ✗ Will Fail | ✗ High Risk | Consider PVC or solid wood alternatives |
Kitchen - General | ✓ Away from Sink | ✓ Recommended | Seal all cut-outs thoroughly |
Under Sink Cabinet | ✗ Never | ✓ With Precautions | Waterproof mat essential; check regularly |
Living Areas | ✓ Ideal | ✓ Over-specified | Standard finishing sufficient |
Utility/Laundry | ✗ Not Recommended | ✓ With Full Sealing | Raise off floor; watch for leaks |
Dry areas (Use Class 1)
Standard MDF performs well in living rooms, bedrooms, hallways, and studies where moisture exposure is minimal. Normal primer and paint provide adequate protection for these environments.
Humid areas (Use Class 2)
Bathrooms
Recommended: MR MDF only, with comprehensive sealing
Suitable for: Vanity units, cabinet doors, skirting boards (with good ventilation)
Avoid: Shower enclosures, bath panels without backing, areas with poor ventilation
Kitchens
Recommended: MR MDF for all applications near water sources
Suitable for: Cabinet carcasses, doors, drawer fronts (away from sink)
Avoid: Under-sink base units, splashback areas, dishwasher surrounds
Installation tip: Even MR MDF requires a gap between the bottom edge and floor in bathrooms. Water pooling at floor level is a common cause of MDF skirting board failure. Use plastic packers during installation and seal the gap with flexible sealant.
"Seal it and paint it with acrylic, urethane or some other oil based paint. If your bathroom floods the trim will be garbage but it will hold up fine in normal conditions."
– Realistic assessment from experience
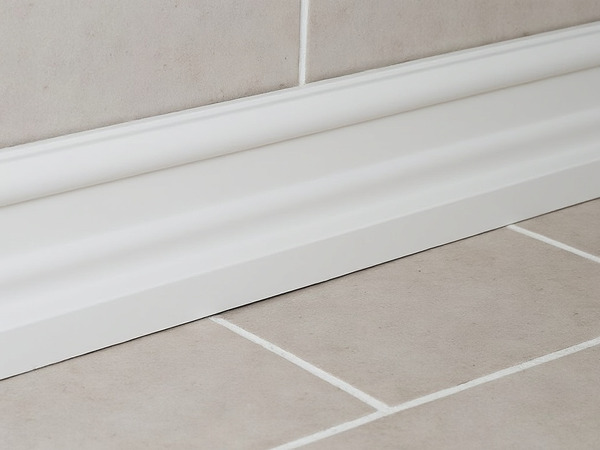
Alternative materials for wet areas
Some applications exceed the moisture resistance capabilities of any MDF grade. In these situations, alternative materials provide better long-term performance.
Application | Recommended Material | Key Advantages |
---|---|---|
Outdoor use | Marine plywood, exterior MDF (Tricoya), treated timber | Weather resistance, dimensional stability |
Wet room skirting | PVC skirting boards | 100% waterproof, no swelling |
Under-sink cabinets | Marine plywood with epoxy coating | Survives plumbing leaks |
Shower walls | PVC wall panels, cement board | Complete water impermeability |
High-humidity basements | PVC trim, composite materials | Mould resistance, durability |
While these alternatives typically cost more than MDF, they eliminate the risk of water damage in challenging environments. The additional investment often proves worthwhile when considering replacement costs and potential consequential damage from MDF failure.
The Bottom Line - Is MDF Waterproof
MDF isn't waterproof, but this doesn't preclude its use in many applications where moisture might be present. Understanding its limitations and implementing appropriate protective measures allows successful use in kitchens, bathrooms, and other challenging environments.
Standard MDF remains an excellent choice for dry interior applications. Moisture-resistant MDF, when properly sealed and maintained, performs well in humid conditions with occasional water exposure. Neither grade can withstand prolonged or direct water contact without protective treatments.
Success with MDF in any environment depends on three factors: selecting the appropriate grade for the conditions, implementing thorough sealing and finishing systems, and recognising when alternative materials represent the better choice. With this knowledge, you can confidently specify MDF where it will perform well and avoid costly failures where it won't.